Inicio » Packaging » Troqueladoras » El proceso de troquelado
EL PROCESO DE TROQUELADO
El proceso de troquelado es un componente fundamental en la industria del packaging y la manufactura, utilizado para cortar, marcar o dar forma a materiales como papel, cartón, plásticos y metales.
Este proceso permite la producción en masa de piezas con formas complejas y precisas, manteniendo altos estándares de calidad y eficiencia.
A continuación, exploramos el proceso de troquelado en detalle, desglosando cada etapa y explicando su importancia técnica.
1. PREPARACIÓN DEL MATERIAL
La primera etapa del proceso de troquelado es la preparación del material que se va a utilizar. Esto implica seleccionar el tipo de material adecuado (papel, cartón, plástico, etc.) y asegurarse de que esté en las condiciones óptimas para el troquelado. El material debe ser cortado a las dimensiones necesarias y apilado de manera ordenada para facilitar su alimentación en la máquina troqueladora.
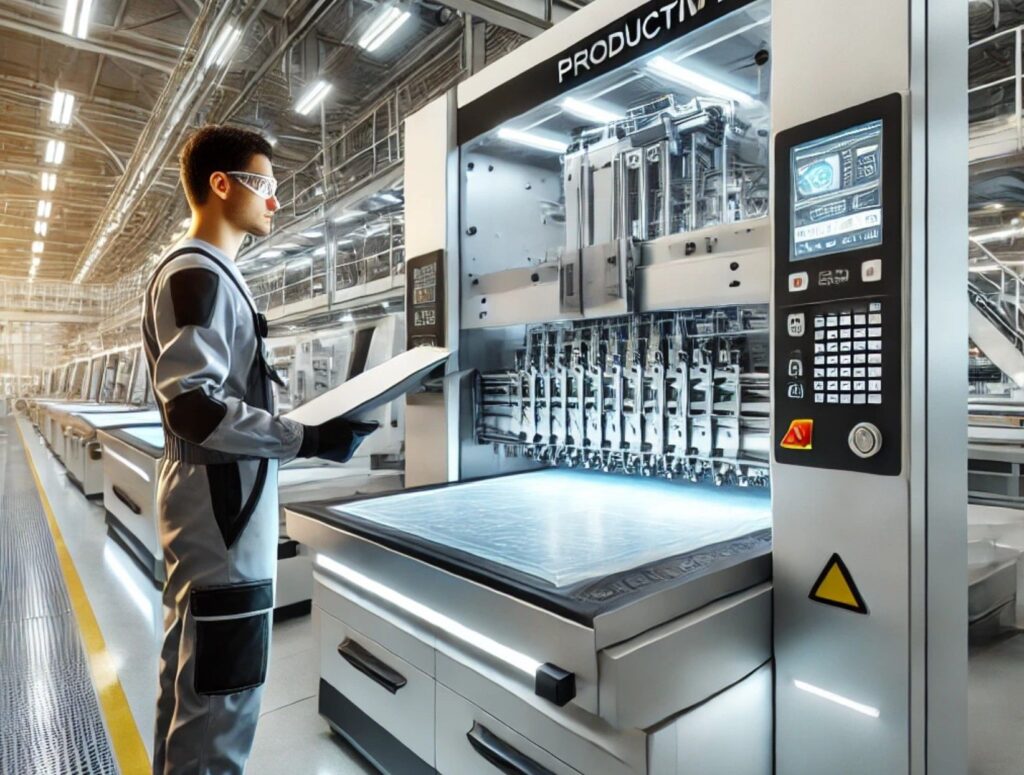
2. DISEÑO Y FABRICACIÓN DEL TROQUEL
El diseño del troquel es crucial para el éxito del proceso de troquelado. Un troquel es una herramienta hecha a medida que corta, marca o moldea el material en la forma deseada. El diseño del troquel se realiza utilizando software de diseño asistido por computadora (CAD), que permite crear patrones precisos y detallados. Una vez finalizado el diseño, el troquel se fabrica utilizando materiales de alta dureza, como acero, para garantizar su durabilidad y precisión.
Existen varios tipos de troqueles, incluyendo troqueles planos, troqueles rotativos y troqueles magnéticos. La elección del tipo de troquel depende del material y del tipo de corte requerido.
Los troqueles planos son ideales para cortes precisos en materiales delgados, mientras que los troqueles rotativos son más adecuados para cortes continuos en materiales más gruesos.
3. ALIMENTACIÓN DEL MATERIAL
El proceso de troquelado comienza con la alimentación del material en la máquina troqueladora. El alimentador, que puede ser manual o automático, suministra el material de manera continua y uniforme a la máquina.
Los alimentadores automáticos son preferidos en producciones a gran escala debido a su capacidad para mantener un flujo constante de material, lo que mejora la eficiencia y reduce el tiempo de inactividad.
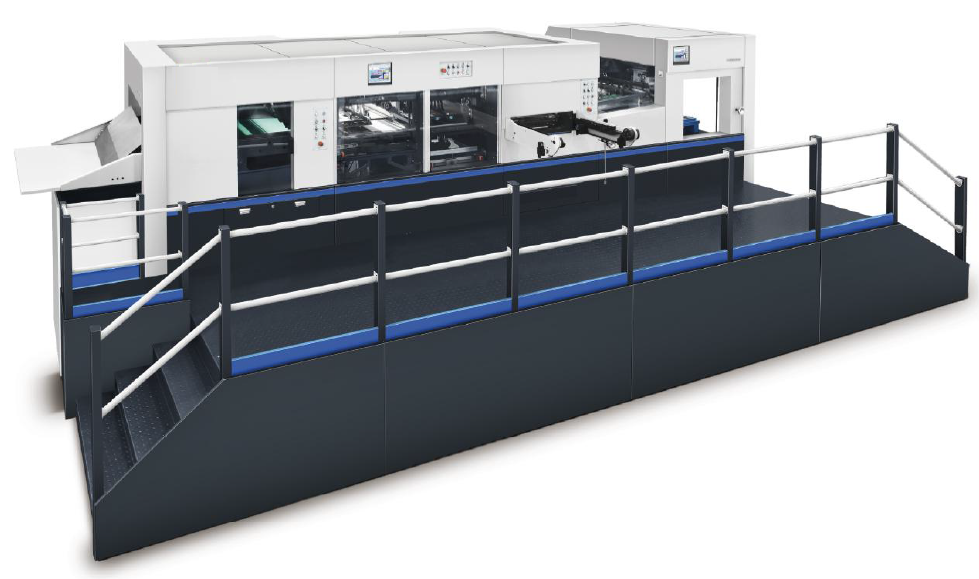
Troqueladora automática 1060 con stripping y separación de poses
Sistema de centrado. Control por PLC y pantalla táctil. Detección de doble hoja mediante sensor ultrasónico. Lubricación automática. Sistema de seguridad mediante dispositivos fotoeléctricos.
4. ALINEACIÓN Y REGISTRO
Una vez que el material ha sido alimentado en la máquina, pasa a la mesa de registro. Esta etapa es crucial para garantizar que el material esté alineado y posicionado correctamente antes de que se realice el corte.
La mesa de registro está equipada con sensores y guías que corrigen cualquier desalineación, asegurando que cada hoja esté perfectamente posicionada para el troquelado.
La precisión en esta etapa es vital para evitar errores y desperdicios, garantizando que cada troquelado sea exacto y consistente.
5. TROQUELADO
El troquelado es la etapa principal del proceso, donde el material se corta o se marca con el troquel. Dependiendo del diseño de la máquina, el troquel puede ser plano o rotativo.
En una troqueladora plana, el material se coloca sobre una superficie plana y el troquel aplica presión desde arriba para realizar el corte. En una troqueladora rotativa, el material pasa entre dos cilindros, uno de los cuales contiene el troquel, que corta el material a medida que gira.
La presión aplicada durante el troquelado es ajustable, lo que permite trabajar con materiales de distintos grosores y durezas.
La tecnología moderna en las troqueladoras incluye controles automatizados que ajustan la presión y el posicionamiento del troquel, mejorando la precisión y reduciendo el tiempo de configuración.
6. ESTAMPADO Y ACABADO
El estampado es una función adicional que muchas troqueladoras incluyen para agregar valor y versatilidad al proceso de producción.
Este permite la aplicación de detalles adicionales, como hot stamping (estampado en caliente) y gofrado, que añaden textura y elementos decorativos al producto final.
El hot stamping utiliza calor y presión para transferir una hoja de metal fino al material, creando efectos metálicos brillantes.
El gofrado, por otro lado, crea un relieve en el material, añadiendo una dimensión táctil y visual. Estas funciones de estampado son controladas con precisión para asegurar una aplicación uniforme y de alta calidad.
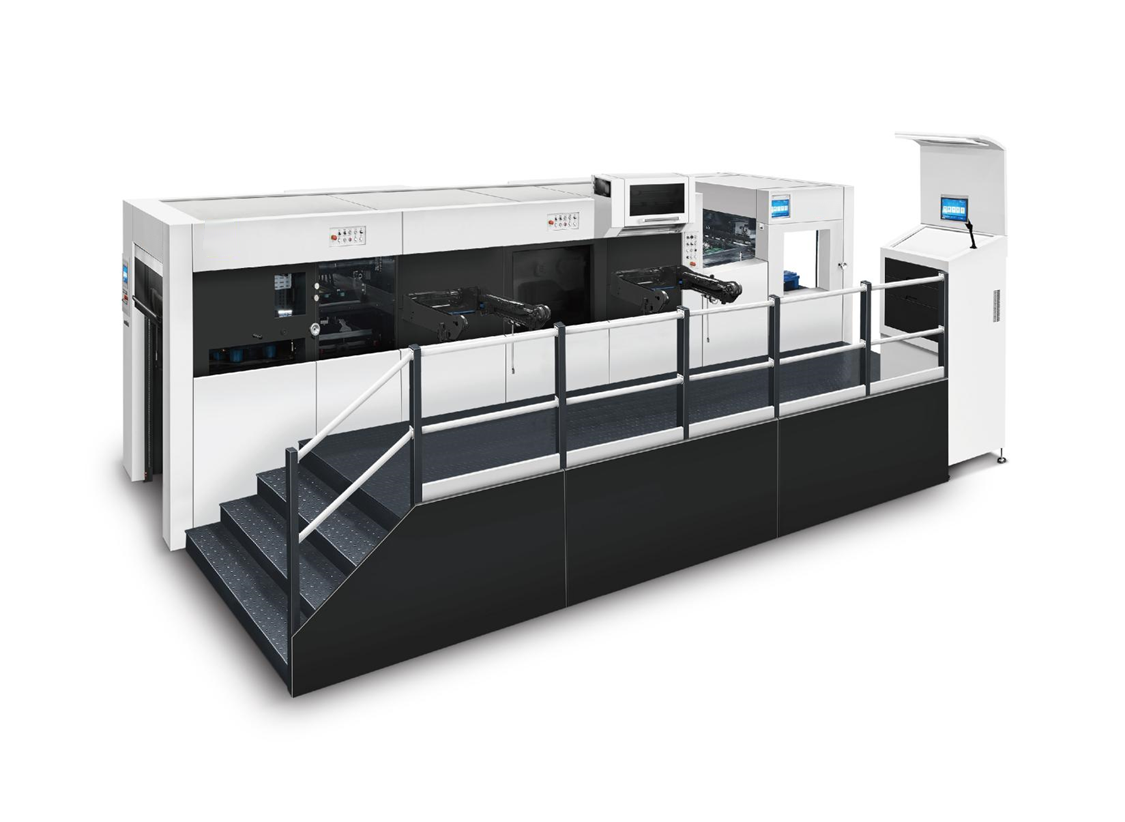
Troqueladora automática 1060 con Hot Stamping, embossing y stripping
Sistema de centrado. Control por PLC y pantalla táctil. Detección de doble hoja mediante sensor ultrasónico. Lubricación automática. Sistema de seguridad mediante dispositivos fotoeléctricos.
7. RETIRO DE RESIDUOS
Una vez que el material ha sido troquelado y estampado, pasa a la etapa de retiro de residuos.
Este proceso, también conocido como pelado, implica eliminar los sobrantes del material troquelado, conocidos como retales.
El pelado puede ser realizado manualmente o de forma automática.
Las troqueladoras avanzadas cuentan con sistemas de pelado automático que mejoran la eficiencia y limpieza del proceso, reduciendo la necesidad de intervención manual y minimizando el riesgo de errores.
8. RECOLECCIÓN Y CLASIFICACIÓN
La etapa final del proceso de troquelado es la recolección y clasificación del material troquelado.
La recolección eficiente es crucial para mantener la fluidez del proceso de producción y evitar atascos o interrupciones.
Existen sistemas automáticos de clasificación que separan y apilan diferentes productos según sus características específicas, mejorando la organización y facilitando el manejo posterior del material.
9. MANTENIMIENTO Y OPTIMIZACIÓN
El mantenimiento regular de la máquina troqueladora es esencial para garantizar su funcionamiento óptimo y prolongar su vida útil.
Esto incluye la limpieza de las partes móviles, la lubricación de componentes mecánicos y la inspección de los troqueles para detectar desgaste o daños.
Además, la actualización de las máquinas con las últimas innovaciones tecnológicas, como sistemas de control automatizados y sensores avanzados, puede aumentar significativamente la productividad y la calidad del producto final.